The Single Strategy To Use For Welding Inspection
Table of ContentsWelding Inspection Can Be Fun For EveryoneThe Main Principles Of Welding Inspection Some Of Welding InspectionTop Guidelines Of Welding Inspection5 Simple Techniques For Welding Inspection
This technique is carried out in a workshop or area while the welding is being done. The points that are aesthetically inspected include the welder's certificate, slag elimination, joint preparation, climate condition, current made use of, and also condition of the electrode. 2- Magnetic Particle Testing This test is made use of to discover any surface or hardly subsurface problems in a weld.Bits of iron are after that put on the magnetic area as well as if there are any type of problems, the particles of iron will certainly construct up around the flaw, which shows where the defect is and also why it happened. 3 Liquid-Penetrant Examining This examination will discover defects in the surface area of the weld like porosity as well as hairline fractures.
A developer is after that applied that will certainly show if any issues show up. 4 Ultrasonic Testing This examination is accomplished by the usage of sound resonances, which are then sent with the welded joint. The signals obtained on a glass screen will certainly identify if there are any kind of flaws in the joint of the weld.
5 Eddy Current Testing This test will reveal very small fractures and is accomplished by the use a circular coil that brings rotating currents, which is placed near the weld. The rotating currents will certainly create an electromagnetic field, which will certainly communicate with the weld and also in turn, create an eddy current.
Welding Inspection for Dummies
The resulting indentation size is described as a solidity measuring table. 8 Harmful Examining This test is a damaging examination that is achieved by reducing the finished weld right into items, this is per the code for origin bend, face bend, tensile examination, and also side bend. It is used to locate slag inclusion, porosity, and also undercutting defects in welds as well as is really reliable.
It's additionally not functional for an individual that is not skilled in the needed treatments to do this job. Analysis of weld qualities includes the size of the weld and the presence of interruptions. The dimension of a weld can be very crucial, as it frequently correlates directly to strength and also linked efficiency - Welding Inspection.
Revealing weld suspensions likewise is necessary because imperfections within or surrounding the weld, relying on their size or location, might protect against the weld from satisfying its designated function. When stoppages are an unacceptable dimension or in an undesirable place, they are called welding flaws, and they can cause early weld failing by decreasing toughness or generating anxiety concentrations within the bonded element.
It is important to pick a welding common planned for usage within the certain market or application in which you are entailed. Weld Examiner Responsibilities Welding evaluation calls for an expertise of weld illustrations, symbols, joint layout, procedures, code and also conventional needs, as well as evaluation and also screening methods. Because of this, lots of welding codes and requirements need that the welding inspector be formally certified, or have the required expertise as well as experience to perform the evaluation.
Welding Inspection - Questions
Right here are a few points that a welding inspector should know and also tasks he must have the ability to perform: Certain procedures should be complied with to qualify welders and welding treatments. The qualification process is an indispensable part of the general welding top quality system, and the welding inspector commonly is needed to collaborate and validate these sorts of certification tests.
These bonded samples normally are needed to be checked after completion. Radiographic, microetching, guided bends, transverse stress, and nick-break fracture are some of the tests that are utilized. The test results have to satisfy or surpass the minimum needs as stipulated in the welding code or standard before the procedure can be certified.
The welding inspector have to be capable of determining all of the various welding stoppages during visual inspection. Welding Inspection. He additionally should have the ability to evaluate, in regards to the relevant welding code or requirement, the relevance of identified stoppages to identify whether to approve or decline them during screening and production.
A welding inspector occasionally is required to perform weld screening by surface area fracture discovery techniques. Additionally, he needs to know just how the tests are used and also what they will certainly discover.
Everything about Welding Inspection
These assessment methods are utilized to examine the inner framework of the weld to develop the weld's integrity, without destroying the bonded element. The welding inspector might be required to understand this kind of screening and be experienced in the analysis of the results. Radiographic as well as ultrasonic weld assessment are both most typical techniques of NDT used to find gaps within the internal framework of welds.
Radiographic screening uses X-rays website here generated by an X-ray tube or gamma rays created by a contaminated isotope. The basic principle of radiographic inspection coincides as that for clinical radiography. Penetrating radiation is travelled through a solid things, in this case a weld, onto a photo movie, leading to an image of the item's interior structure.
Power not taken in by the object will cause exposure of the radiographic movie. These areas will certainly be dark when the film is established. Areas of the film exposed to much less power remain lighter. Flaws within or adjacent the weld might stop the weld from fulfilling its intended feature. Consequently, areas of the weld where the density has actually been transformed by stoppages, such as porosity or fractures, will look like dark outlines on the movie.
A beam of light of ultrasonic power is routed right into Visit Your URL the weld to be tested. This light beam takes a trip through the weld with unimportant loss, other than when it is obstructed and also mirrored by a discontinuity.
The Main Principles Of Welding Inspection
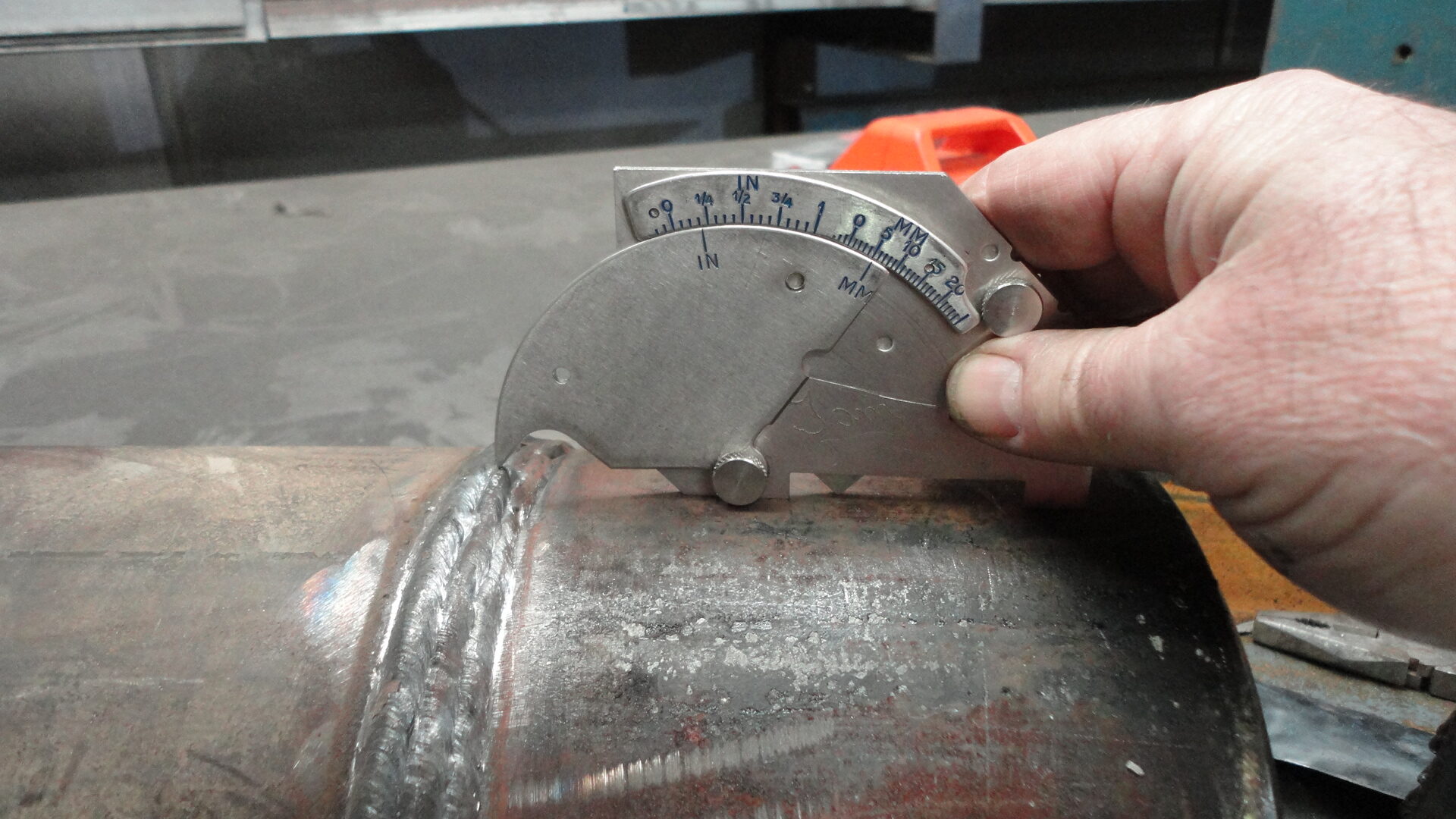

Several of these tests are the led bend test, macroetch examination, minimized section tensile test, crack test, and also Charpy V-notch impact examination. These examinations are utilized throughout welding procedure or welder performance qualification screening. The welding examiner typically is called for to carry out, monitor, or review these testing methods. The welding inspector must be skilled in the capacity to read engineering and also manufacturing drawings, and also be able to interpret all information and also symbols that offer information concerning the welding requirements.
If you have little or no previous welding experience we advise that you go to the CSWIP Visual Welding Examiner as it will assist you get ready for future presence to the CSWIP Welding Assessor training course. The CSWIP Welding Examiner program is created for examination designers and also managerial team. If you call for some practical welding knowledge to aid enhance your understanding of the examination of welded products, please take into consideration the CSWIP 3. You have to hold website link this degree for a minimum of 2 years prior to moving to the next degree. You have to hold the CSWIP welding assessor degree for a minimum of two years prior to relocating to the following level.